新開発転造盤によるヘリカルインターナル歯車の成形
―精密自動車部品に対するインクリメンタル成形の適用―
はじめに
歯車加工法は大きく歯形を創製するための工法と粗製作された歯車の精度を向上させる目的で採用される仕上げ工法に大別される.外歯車における歯形創製法としてはホブ盤による歯切加工がいまだ一般的である.
自動車製造分野に限って見渡しても,長年研究されてきた塑性加工法(冷間鍛造)はスタータモーターとリングギアをつなぐスタータピニオンの押出し成形に始まり,最近の閉塞鍛造によるデファレンシャル用傘歯車や分流を活用した遊星歯車機構に供されるプラネタリーピニオン,あるいは電動パワーステアリング機構に使用されるウォームピニオンの製作など幅広く採用されてきた.図6に過去に量産に共されてきた冷間塑性加工歯車例を示す.ただし,最も多くの歯車を使用しているマニアルトランスミッション用にはそれほど多くの冷間鍛造歯車が採用されたという報告を聞かない.
翻ってオートマチックトランスミッションに多用されている遊星歯車機構に目を転じると,主要部品のひとつである内歯車は歯形創製のための工法としてはブローチ盤による切削が一般的である.もちろん,プレスによる押出工法も25年以上前から報告され,近年さらに改良されて量産加工に適用しているという鈴木正氏らの報告[1]もあるが,ブローチ法にしろ押出し法にしろ歯車デザインが貫通している場合に限られコップ状形状には採用できない.
ブローチ盤によって製作されている内歯車の大半は後加工によってフランジと結合され,結局はコップ状の内歯車として使用されるものと認識している.フランジと一体となった内歯車の歯形創製はギアシェィパーによる歯切加工かプレスによる冷間鍛造による以外ないが,オートマチックトランスミッションに採用されている上記内歯車のピッチ径は100mmを越え,この大きさはプレスによる冷間鍛造部品としては大型に属し,荷重,精度,型費,いずれの面でも容易ではない.冷間鍛造工法は後述に紹介する場面での本転造工法との共存は考えられるが,単独で満足な結果に到達したとの報告には接していない.
ギアシェィパーによる当該部品の量産加工は唯一可能な製法であるが,加工時間,加工精度両面で不満が残ることは否定できない.
一方,小生は松原茂夫氏の提唱された逆張出し成形[2](2.5次元NCフライスを用いた板金の3次元NC成形)に大変感化され,その実践に携わった経験があり,この究極のアイテムともいえる内歯車の成形にインクリメンタル加工をもって対応することを考えた.
前述の歯車仕上げ工法として,最終精度にかかわる場面でシェービングとともに登場するローリング(仕上げ転造)は精度の面ではそれなりの評価を得,業界で認知された機械も販売されている.もし転造で歯形創製が可能となれば他の工作機械はまったく不要となるわけでその効果は絶大である.図1に本開発工法で製作した内歯車を示す.
図1 転造ヘリカルインターナルギア(一部拡大)
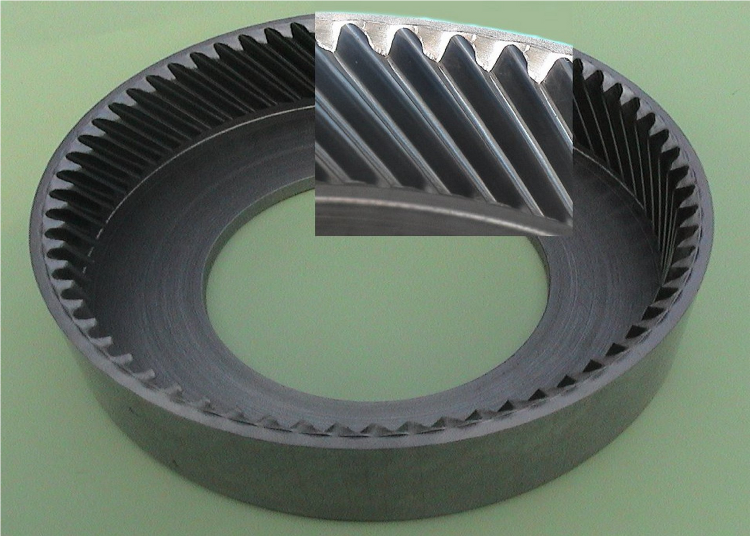
奇しくも転造は大型部品を成形するにあたり,面積で要求されるプレス荷重の部分を周長と称する長さ(インクリメンタル加工としては時間)の関数にいわば微分してくれる訳で,1000トンを1秒間というプレス加工の代わりに30トンを30秒間というインクリメンタル加工は機械設備の小型化(省投資額)という面で大変魅力的である.
(内)歯車転造の現状
先に触れた通り,歯車の転造に関係する報告は外歯車、内歯車にかかわらずいわゆる仕上げ転造に限られているようで,内歯車の歯形創製転造分野に限ればドイツ国PROFIROLL TECHNOLOGIS社から提案され,EMOショー(ドイツ,ハノーバー市)においては実演も公開されている技術[3]が唯一のようである.これとて,いかなる精度の歯車ができているのかの報告には接していない.
図2 新開発転造盤の主要部
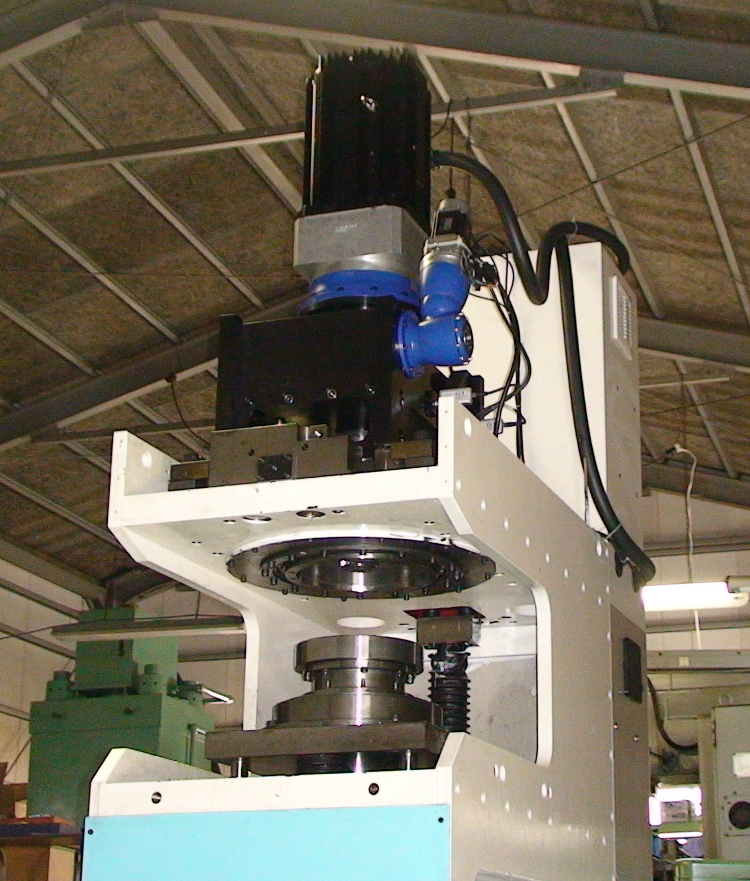
このP.T.社の方法は被加工材と転造工具の回転は機械による同期運転がなされている点で弊社提案とは大きく異なる.
そもそも、歯車工作機械業界全体に存在する常識として,被加工材と(刃物であれ砥石であれ)工具の動きはある関係における同期が必然であり,この同期運転なしに正確な歯溝の創製は有り得ないとしているようである.
上記以外にグローブ法やフローフォーミング法があり,まさしくインクリメンタル加工であり,転造の範疇に入っているようではあるが,高精度の歯車に適応するという報告(あるいは宣伝)もなく,宣伝にある多板クラッチのハブやドラムに関しては納得できてもその延長線上に歯車があるとは思えなかった.
コップ状素材を芯金に被せて外側からアクセスする工法は,ベアリングの内外輪の製作に活用されているリングローリング法でも明白な通り,その転造の進行とともに素材肉厚は薄くなり,いわばそのピッチ径は次第に大きくなってゆく.この被加工材が縮径的に芯金に密着しその形状を精度良く転写するとは思えなかった.
新工法の発想と転造盤の構造
剛性の高いコンテナの採用
前述リングローリング法は大型部品を軽荷重で成形する点で大変魅力的な工法ではあるが真円度を創製あるいは保持するには拘束が不足していることに着眼し,素材外周をコンテナで拘束することは必然だと考えた.
図3 新開発転造の構造(クリックで拡大)
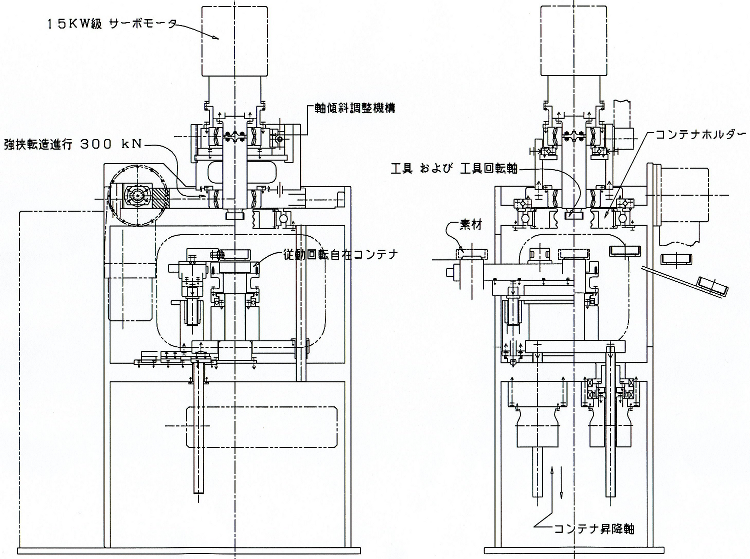
冷間鍛造で歯車成形を経験していたので,一様内圧が作用する鍛造の場合以上に円周の一部の荷重を全周に施してゆくインクリメンタル加工において真円度を保持するにはかなりの肉厚のコンテナが必要であると思考した.剛性を志向するかぎりこのコンテナには構造の複雑なコレットチャックがごとき積極的把持機構はそぐわず,平滑な内周のコンテナに平滑な外周の素材を整合挿入することになった.
ここに至って如何なる機構を持ってしてもコンテナの中で回転自由に存在する素材の回転を制御することは不可能になったので必然的にこのコンテナ自体も従動回転自由となり,従来の歯車工作機械にはない特色を得た.
弊社特許[4]の公開後の申請とはいえ,前述P.T.社出願特許とも明白な差別を主張することになっている.
新開発転造盤の構造
前記特徴を盛り込んだ試作転造盤の外観を図2に,本格量産対応機の構造を図3に示す.サーボモーターで駆動するNC軸から増力ウエッジを介して最終的には300kNの転造挟圧力を発生している.300kNものラジアル荷重に対応する片持支持の工具回転軸には,当然,曲がりたわみが発生する.本機においては大口径コロガリ軸受けを2箇所に配し,サーボ機構で工具軸の傾斜を自由に制御する機構を採用している.
この機構により転造応力でたわんだ工具軸および工具歯車と加工中の素材内周の関係が然るべき位置関係を保つべく制御されることになる.この機構は製作する歯車にクラウニングを設けることにも活用可能であり,90度方向にも設置された同様の機構は工具歯車と製作する歯車の間に発生するネジレ角の乖離の修正をも可能にしている.
図4に工具歯車の一例を示す.
図4 転造用工具歯車
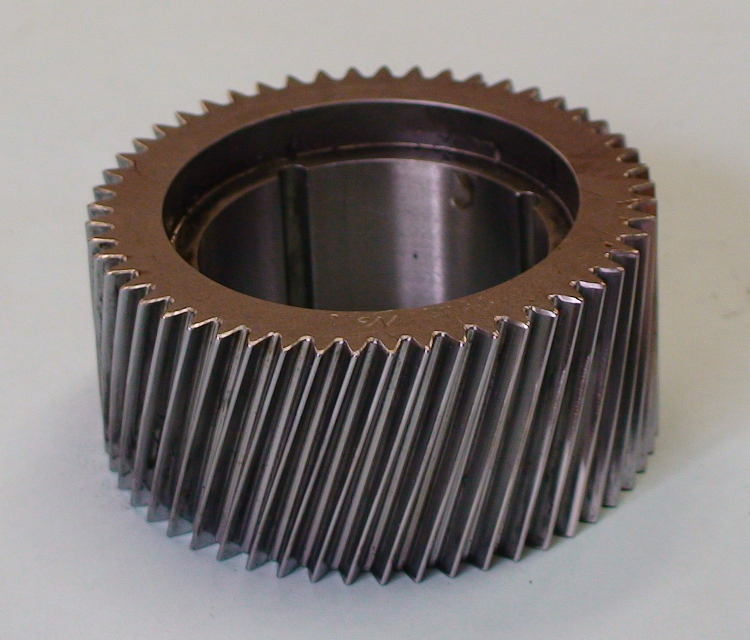
また,下部からの素材のチャージ機構は素材を格納したコンテナを工具歯車に対応する位置まで押し上げることと,大口径のラジアルベアリングを介して待ち受ける部材で素材の上端面を拘束すること,さらには下降途中での加工完了品の突出し任務をも引き受けている.出力は2本のサーボボールネジでトータル120kNを発生する.
転造挟圧力はサーボモーターの電流値で確認できる.転造挟圧力を生む機構として採用したテーパウエッジは剛性が高く,転造負荷変動にかかわらず一定の肉厚生成を行うことに貢献している.
固定側であるコンテナ回転軸受部に対して工具軸受部を包含するテーブルを強制的に移動させることが転造の進行そのもので,その進行はテーブルの位置をミクロンモニターすることで把握可能であり,この数値は加工品のオーバーピン径と連動する.この把握再現精度は20ミクロン以下で現実の歯車に要求される許容範囲を充分まっとうできる.
転造の条件と転造歯車の諸元
図5に歯車精度検査表を示すサンプルの概要を説明する.
試作用素材はSCM 420(焼鈍材、75 HRB)で丸棒から削り出した.
工具回転速度は減速機つきサーボモーター制御で最高回転数は250RPMである.加工時間は精度向上を目的としたスパークアウトを含めて約50秒を費やしたが,このタクトでは転造品の温度上昇はネグレティーブであった.また,この生産タクトはプログラムの熟成で半減する余地を残している.
- 転造歯車の諸元は次の通りである.
-
モジュール 1.50
歯数 64枚
ピッチ径 110.85
圧力角 20度
ネジレ角 (右)30度(計測時29.8度)
歯幅 28mm
転造工具の設計
オーバーピン径と歯底径の関係は工具により決定されるため工具歯車はその歯先が被加工歯車の歯底を所定の寸法にしたとき歯厚も設定値になるよう設計しなければならない.事前設定の歯車仕様にフィットする工具の設計には少々ノウハウが存在するがすでに試みをされている顧客の機密に触れることになる.ただし,被加工材歯車と工具歯車の間には歯先,歯底いずれにもクリアランスが存在しない点を除けば常識的な歯車知識の範囲にあると理解している.また工具歯車には自由は許されるのでその再研削も可能であると考えている.
ただ,転造完了時の歯車諸元に対応して設計した工具歯車が転造初期の正確な歯数割出しにそのまま対応可能かといえば率直に言って難しい面がある.今回発表の実績には割出しのために設計した予備転造用歯車を用意し,転造を2工程とした.
均等割出しのための予備転造
なんら手掛かりのない平滑内周に正確に均等な歯溝を刻むためには,本歯車と素材が接した直後における同調ピッチを主眼にしたこの予備転造用工具歯車の設計と,本工具歯車が素材と接した直後の運転パターンに工夫が必要である.いずれにしろ,個々の状況にふさわしいサーボプログラムを見つける必要はあり,工具設計だけに重点があるわけではない.ここでは再現性の高い定量分断が可能であったことと,最も懸念された素材内径の絶対値や肉厚の幾分かのバラツキは容認されることが確認されたことを報告する.
この予備転造用工具歯車から引続き供される本転造工具歯車への引継ぎは本工法の最大の難点ではある.大方の予想通り,理論的には成立しない歯車同士の噛合いであり,変形自体が転造の進行なので変形は当然許されるが,せん断や破断は許されないという微妙なバランスをクリアーする必要がある.ただ,予備転造用工具は,受渡しがなされる両工具歯車の歯先近傍のネジレ角にさえ配慮すれば,歯形(圧力角)や歯タケはもちろんモジュールさえも自由に設計可能であり,このため、予備転造の代わりにプレスによる押出しで成形したインボリュート歯形とはまったくかけはなれた形状の歯溝を設けた素材からも試作したが精度に優劣は現れなかった.
創歯転造についての知見
予備転造(あるいはプレスによる溝成形)を経た素材を最終的に歯車に作り上げる過程を2つに分けて説明したい.
ひとつは挟圧転造によって所定のオーバーピン径を得る(結果として歯底径を作る)過程で,創歯転造と呼びたい.創歯転造こそ本工法の核心というべき部分で,その時点での歯車精度を図5に示す.
もうひとつは創歯転造完了後,当該工具歯先と被加工歯車の歯底の間に若干でもクリアランスを設け,歯面同士の接触だけで回転を続けることで,今回はこれを仕上げ転と呼ぶ.今回の発表にはこの部分での試行は反映されて造いない.
図5に掲げる成績表以上の歯形精度を求めていくと,この仕上げ転造領域に工夫が凝らされることになろう.すでに弊社の需要家においては一定のレベルに達しているように聞いている.
結果と評価
図5に歯車検査票を掲載する.アイテムのネジレ角は30度である.ご覧のごとく,強ネジレ角であっても新工法歯車のピッチ精度はほぼJIS1級で,充分実用域にあるとの評価を得ている.図1の転造ヘリカルインターナルギアの拡大写真にあるごとく,歯面の面粗度のよさは特筆ものであり,歯先の丸みも含めて成形されている.また,歯車端面の性状も良く,バリ取などの後加工の廃止も視野に入っている.歯形誤差に関しては片側に改善の余地が認められるが,いずれ前述仕上げ転造におけるノウハウが解決するであろう.
前回(平成21年5月学会発表時)の報告において「最も問題が残るのは歯スジ誤差(ネジレ角誤差)といえる」と述べたが,今回掲載した新しい転造盤は前述したとおり機械にこのネジレ角修正機能を盛り込んだので完全に解決した.さらにこのネジレ角微調整方向に工具軸を傾けることは工具固有のピッチを見かけ変更できることでもあり,前述受渡時の問題解決の一助にもなりうる.
図5 転造歯車の精度検査表(クリックで拡大)
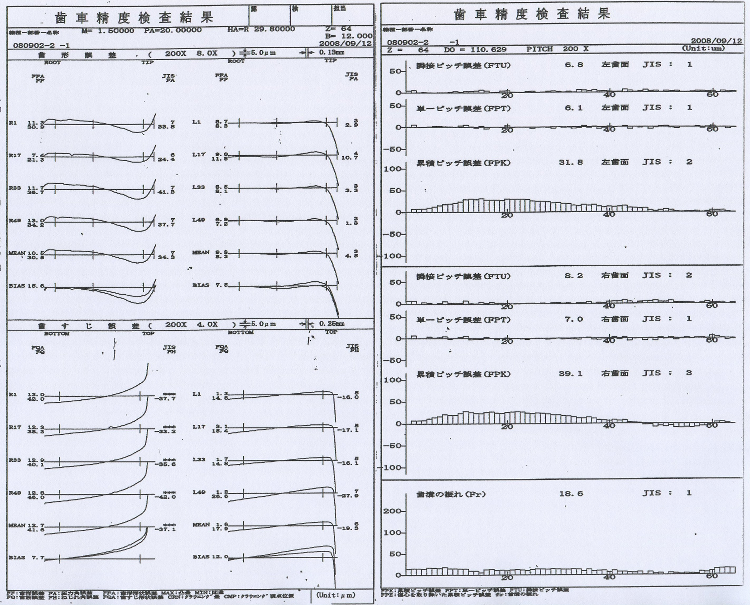
まとめ
前述の本格的量産を目した転造盤による転造品は,精度的には実用レベルの歯車を生産する手段として認知されつつあり,その転造時間としては,種々の条件設定のための習熟期間を経過した後は予備転造,創歯転造ともに各30秒というところが期待されている.設備および工具費用の低廉さとあいまってヘリカルインターナルギアの製造コストは激減するであろうと考えられる.
本技術は歯車製作技術としても,例えば基礎円ネジレ角の概念がない(らしい)こと,すなわち軸直角見掛け圧力角のスパーギアの積層モデリングであろうことなど小生の理解の範疇を越えたご意見も頂戴しているが,ともかくマスター歯車ともいえる工具歯車と滑らかに回ることが確認されている唯一の歯車創製法であることは否定し得ない.
本技術の活用可否は塑性加工技術以上に歯車技術の部分に大きく依存しそうである.工具寿命を含めて転造で作る歯車はいかなる諸元が有利不利であるかはこれからの問題である.小生の当面の作業はいかにしてさらに強度の高い工具を提供できるかに向かっている.
図6 冷間鍛造による歯車例(参考)
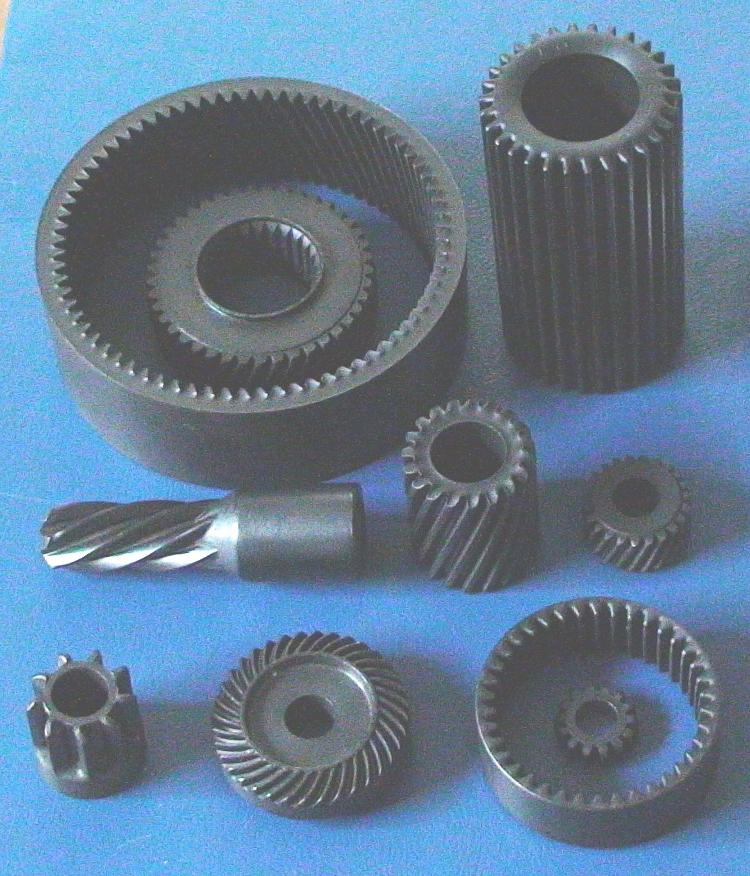
工具と被加工材の接触部の有限要素法的応力場解析や,歯車創製過程における疑問「工具が歯形を作るのか,それとも軌跡がインボリュートを保証するのか」について諸先生のご意見を頂戴したい.
内側に凹凸をもつ多板クラッチのドラム,シンクロスリーブ,等速ジョイント部品等への展開も試作段階にあり,また,粉末焼結品を供給素材としてその密度,強度の上昇を図る分野も期待されている.
さらには自動車部品分野に限らず,もっと大型の遊星歯車機構付き増減速機におけるインターナルギア(例えば風力発電装置用)の製造にも適応できないかなど,小生も思いも及ばなかった分野からの引合いもある.
ところで本転造盤のコンセプトは弊社既販売中の塑性加工用プレス機と同じくコンパクト且つ低騒音であり,大きさがテーブルサイズのピットレスであることはもちろん,作業振動皆無,運転音は75db以下と他の歯車精密加工機との共存や前後加工工程用工作機械とのインライン接続にも支障なくフィットすることをお約束するものである.
最後に,小生が最初に歯車転造の手ほどきを受け,貴重なご指導をいただいた元山形大学の植松整三博士をはじめ本件開発にご協力いただいた諸先輩に紙上を拝借してお礼を申上げたい.
参考文献