新開発転造盤によるヘリカルインターナルギヤの成形
緒言
表題はヘリカルインターナルギヤ(第1図)の転造成形についてとあるが本稿ではこの内歯転造盤の活用を含むトータルな塑性加工システムとして「インテリジェント加工システム」を提唱し、その詳細を説明する。その成果の評価は何と言っても加工品の精度であり、それを客観的に判断して頂くには歯車を選ぶのが最適であると思うと表題から逸脱しているとは言えない。
過年、経済産業省が出した「ものつくり基盤技術の高度化に関する指針(筆者なりに短縮)」の高精度ヘリカル歯車に係る部分を第2図に示す。ここには外歯車を対象としてはいるが歯車成形技術の現状を正確に捉え、将来のための指針が明白に提示されている。本稿の最後に説明する「インテリジェント加工システム」による加工品の精度を評価されるにあたって参考にされると有意であろう。
同様に、同じ指針に「金型、鍛造設備のコンパクト化(第3図)」が打ち出されており、その内容も筆者を大いに奮い立たせたものである。このご指導に沿って従来のプレスを根本的に見直すことから「インテリジェント加工システム」が出発し、プレス加工だけでは克服できないと感じた点のために新開発内歯転造盤が生まれたと言える。
キーワードのインテリジェントの具体的な点は操縦桿であり、大砲がミサイルに変わる点と同じく加工あるいはシステムの進行中にモニターした情報を駆使して操縦し軌道修正を可能としたことであろうか。コンパクト化、静粛性、高剛性、等々ハードの面で機械が進歩するのは勿論であるが、近年趨勢のサーボモーター化はその最大の特徴を運転パターンの模索に使うだけでなく加工道中の軌道修正にまで活用することを提唱したい。
以上のようなストリームの中の一断面としてヘリカルインターナルギヤについて考察する。
図1 転造成形によるヘリカルインターナル歯車の写真
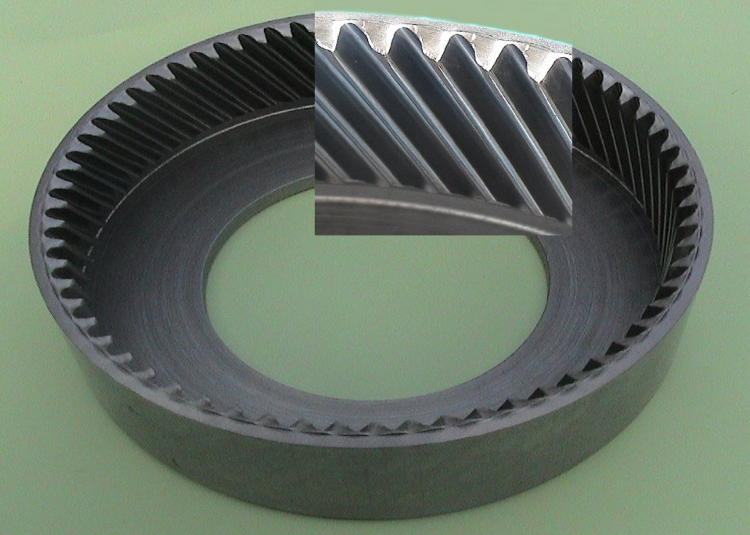
ヘリカルインターナルギヤ
ヘリカルインターナルギヤの主用途は遊星歯車機構(第3図)である。その機構はサンギア軸とその外側に接する複数個の遊星歯車を束ねるキャリア軸、更にその大外を受持つインターナルギア軸からなり、3軸のいずれかを固定し他を入出力軸として利用する同軸増減速機、あるいは入力軸以外のどちらかを制動することで回転方向を切り替えるクラッチとして活用するもの、さらには入力軸以外の2軸に所定のトルクあるいは回転数を配分する差動装置としても使われる。
例えば普通乗用車における自動変速機やハイブリッド車のモータとエンジン軸の間に配置せれる遊星歯車機構においてはクラッチ機能が多用され、車輪ごとにモータを配置した電気自動車では高速回転が可能な小型モータのトルクを増大する減速機として用いられ、4輪駆動車においてはその前後輪に適切な回転トルクを配分するトランスファーに使われている。
図3 遊星歯車機構
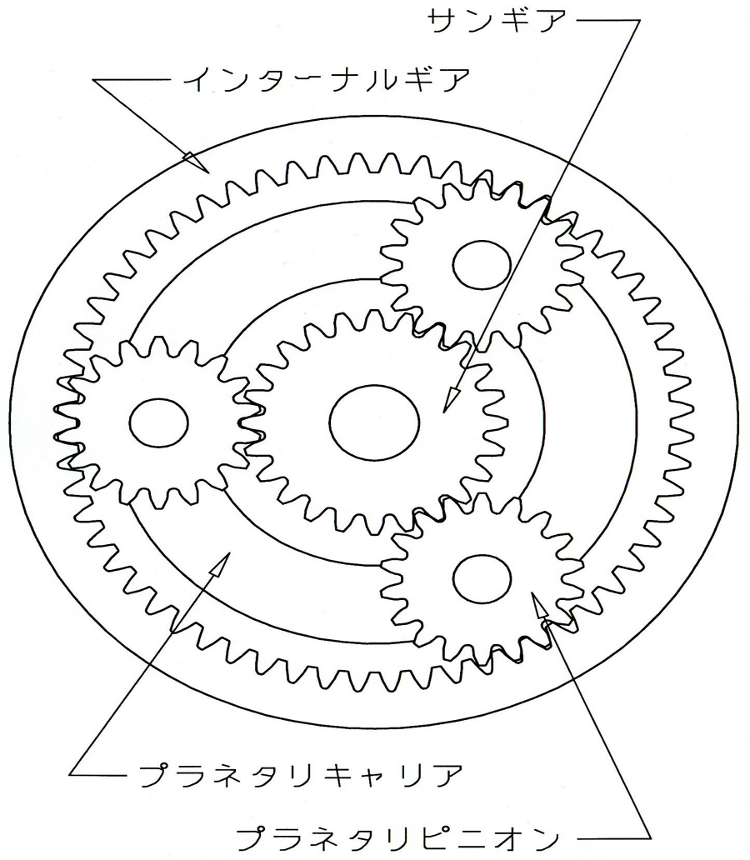
構成するサンギアと遊星歯車は外歯車で、その製作手段は、最初に歯溝を作る創歯工法としてのホブ盤による歯切加工と焼入れ後に精度を保証する歯車研削加工が確立し、塑性加工による創歯技術の活用はいまだ限られた一部においてのみである。(第2図参照)
同じく主要構成部品であるインターナルギアにはホブ盤のごとき常套手段が存在しない。また、焼入れ後のインターナルギアの歯面仕上げ工法としてはホーニング以外に有効な手段がない。従って焼入れ前に高精度が要求されるのが宿命である。
第4図にインターナルギアの加工法を列挙する。最も多用されているブローチ加工は貫通形状に限られ、設備費用、工具費用などにも難点が残る。貫通形状は何らかの後加工でトルク伝達の工作(多くは別品のフランジを装着する)を必要としコストを押上げている。他の工法も一長一短である。
筆者らは数年来、インクリメンタル塑性加工によるインターナルギアの転造成形を提案し、世界20カ国以上の特許[1]を取得すると共に、日本塑性加工学会の学会誌「塑性と加工」[2]に発表している。
図4 内歯車の加工法一覧
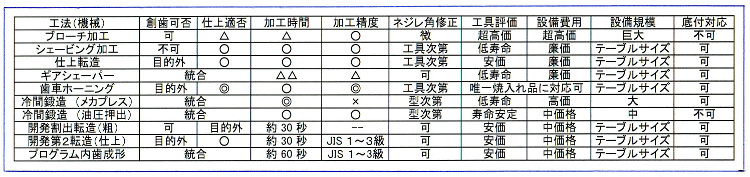
図5 ブローチ加工歯車の実用構造
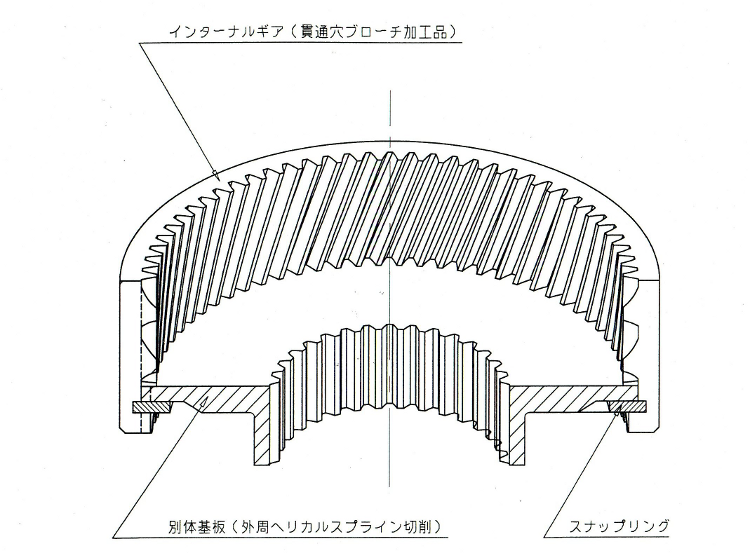
転造工法の要点
転造盤の主要部を第4図に、その基本的な加工要領を第5図に示す。リング状の被加工材の内側から例えば外歯車状の駆動回転する工具歯車(第6図)を半径方向(第5図中X軸方向)に強く押付け被加工材の内側に凹凸を成形するもので、後述諸元のヘリカルインターナルギヤ成形の場合おいては「平均接触面圧1500MPa(推定)」から発生するトータル100kN にもなるラジアル荷重を剛性の高いコンテナとの間に挟んだ素材に与えることになる。このコンテナが被加工材の外径寸法を保持し、その真円度を保証する。
図6 転造盤の主要部写真
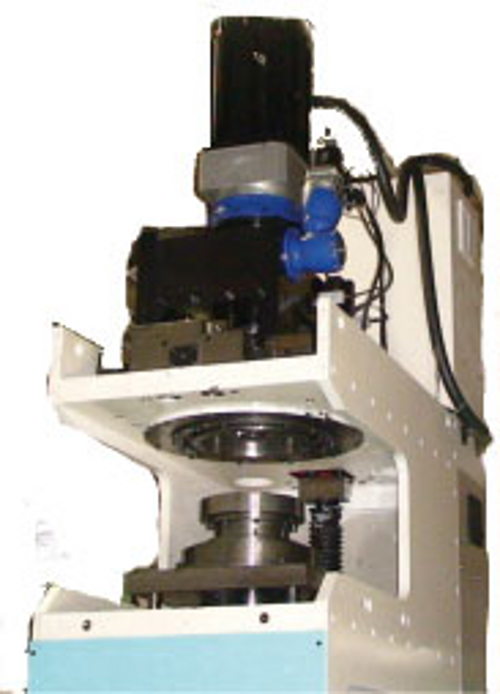
図7 歯車転造の基本概念
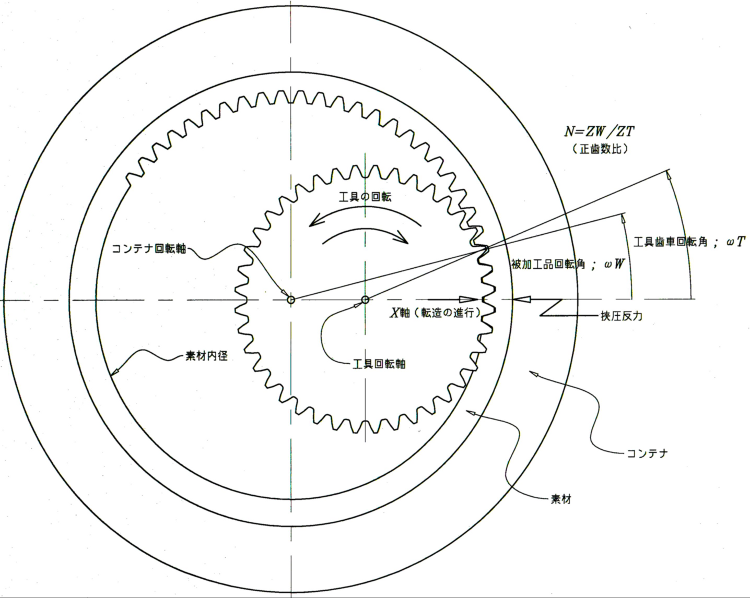
図8 工具歯車の写真
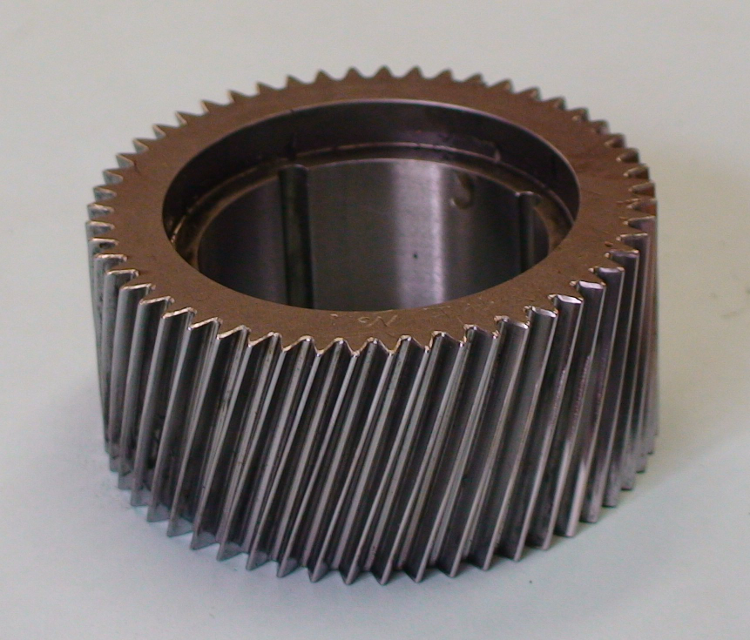
図9 コンテナ部の写真
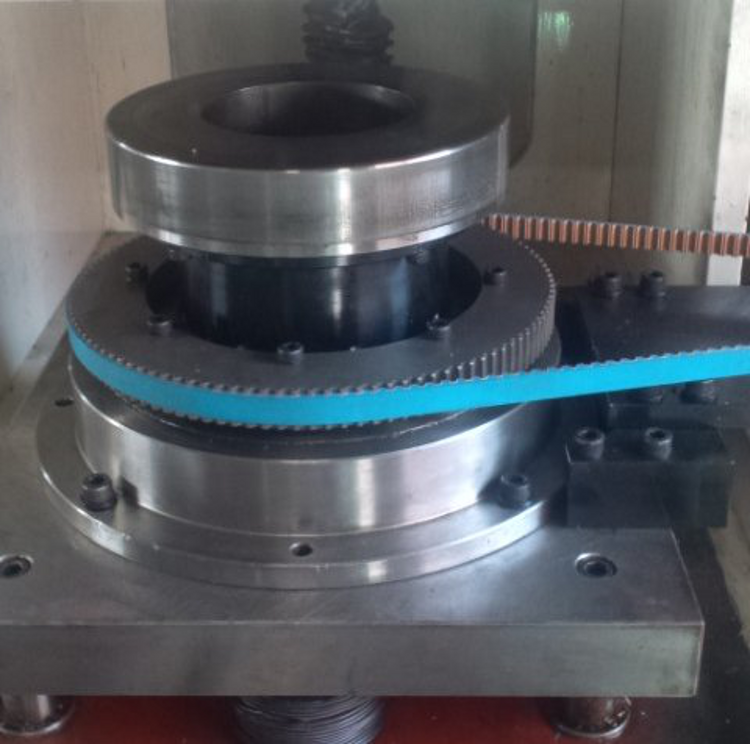
転造盤の詳細説明
前述のアイテムに対応するべく設計された転造盤の特色は、
- 本転造盤の工具軸の軸受構造を片持ち保持としたためブローチ加工では対応出来ない底付き形状も加工可能とした。
- 工具軸のX軸方向の推進機構にテーパウェッジを採用した。この結果なんらかの原因で発生する加工反力の変動に対し工具軸とコンテナ回転軸の軸間距離を剛性高く維持することを得た。また、副次的に小さいモータで大きい力を発生することにも寄与している。
- 工具軸にかかるラジアル荷重によって発生するタワミは如何ともしがたく別駆動の修正制御軸を必要とした。前述X軸同様、テーパウェッジを用いて工具軸を保持する2か所の軸受のうち工具軸回転用モータ側を強制移動させることによりそのタワミを回復させる構造を採用している。この結果BBDのなす円筒の傾斜は制御可能となった。
- 工具歯車のネジレ角と成型された歯車のネジレ角が常に一致するとはかぎらない。本機にはX軸と直角方向(いわばY方向)に工具軸を傾斜修正する機能を盛り込んだ。ただし、この軸はいまのところプログラム運転の対象とはなっていない。
- コンテナ内に整合挿入された被加工材をZ軸の所定の位置に運び、かつ、転造加工中にあるいは発生するZ軸方向荷重の反力を受けその位置を保持するためのZ軸昇降機能を持つ。この軸は転造成形中の被加工材のいわばσ3を作ることで圧力場の制御にも活用される。更に、この軸は成形完了後の被加工材をコンテナから突出すことにも使用される。
図11 転造盤の構造
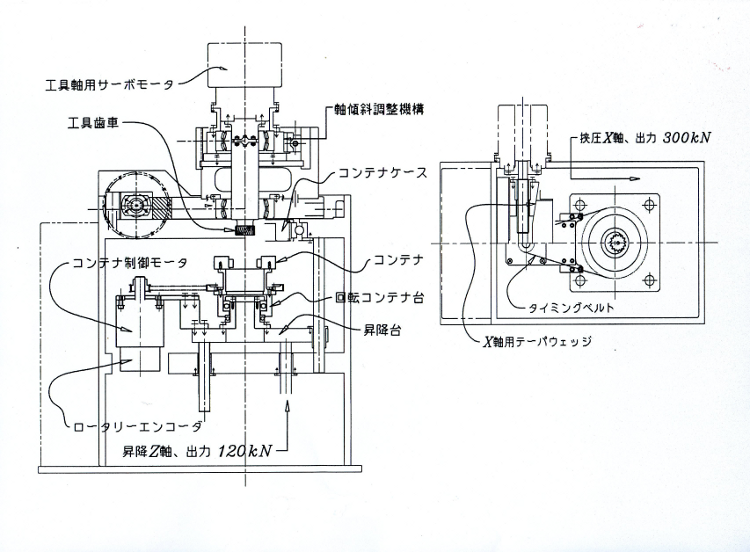
初期割出に関する考察
「完全に平滑な内周を有する素材に所定の歯数の歯溝を正確に刻む」というのが本工法の開発当初からの最大のテーマであり最もご理解頂き難いテーマである。
一定方向に回転している工具歯車にコンテナ内の被加工材を押付け、自然に上記テーマがなされるにはあまりに工具設計が窮屈であり、重要な因子である素材内径が変化すると貴重な工具を破棄せざるをえなくなる。
この状態をとりあえず解消したノウハウを以下に説明する。
第5図において工具歯車がもつ何らかのひと歯あたりのドライブピッチをPTとすると、PTの歯数倍(N倍)に一致する仮想半径RFは素材内径ROより大きい値で素材内の何処かに存在させることは工具設計上それほど困難ではない。この工具を割出用工具という。
この工具歯車と素材の接触初期にX軸を強制的にPF=N・PTが成立するらしき位置まで食い込ませた後、工具歯車によるデバイディングを開始することである。この時ただX軸を進めるだけではなかなか工具は食い込まない。工具軸を2~3歯の範囲で反転揺動させながらX軸を進め、その後も「行きつ戻りつ」を繰り返しながら素材一回転に至るなどの工夫は必要である。
それにしても成立するらしき位置はデバイディング完了までは確認不可であり、せいぜい数回の試行の内に一見美しく歯溝が刻まれたかに見えるまでは到達してもJIS1級の歯溝の振れを獲得するのは容易ではなく、歯溝の成形が丁度一周して過去に成形した歯溝に重なる部分は「特異点」として後々まで我々を悩ませた。
正確な歯溝の割出し
-
今回の開発はハード的にはコンテナ回転をモニタリングするロータリーエンコーダを追加設置することから始まった。(第7図参照)
X軸を前述PF=N・PTが成立するらしき位置まで強制的に食い込ませ、数歯の歯溝を成形した時点で浮動起点的に工具回転角度とコンテナ回転角度を比較し、正確なデバイディングを確認しながら隣接する歯溝の成形を進めれば良い訳で、誤差を確認すれば遡ってX軸位置を修正すればいい。(N-1)歯に関してドライブとドリブンの関係を把握したのち特異点に踏み込めば特異点は消滅するという訳である。正確な歯溝の割出しに寄与する操縦桿を持った所をインテリジェントと言いたい。
この結果第8図に示すごとくこ歯溝の振れはJIS1級を確保している。このアイテムの諸元はモジュール1.50、歯数64枚、ネジレ角30度である。 -
ロータリーエンコーダと共にサーボモータを搭載したので工具と被加工材の系合を一時的に解くことと、工具回転軸とコンテナ回転軸のどちらか一方あるいは両方を制御空転させ、任意の組合せで再度の系合をセットすることで工具の円周の一部を被加工材の全歯に対応させることなどが可能となった。
この機能は異質な3の倍数の内歯をもつシンクロスリーブの製作には特段の威力を発揮し、工具歯車の歯数が製品歯数の公約数から開放され強度重視の工具設計を可能とするとともに、工具の外周に複数のエリアを設定し、本来の仕上げ転造用諸元部分以外に、割出機能部分、中間形状部分、端面成形機能部分などを配置し、被加工材に自由に作用させ、工具交換もなく一度のローディングで複数の加工工程を完了させることも可能とした。
また、工具の回転という転造の基本ともいうべき点でも変化があり回転軌跡が成形品の形状に悪影響するクラッチドラムには放射方向の運動のみで仕上げられた溝を提供可能となった。 - サーボモータのトルク制御機能を利用し、工具の回転に対しコンテナ回転を援助させることやブレーキをかけることも任意となり、工具と被加工材の歯面の接触圧をコントロールすることもできる。この機能はこの機械でシェービングや焼入れ後の歯車にホーニングを施す場合に有効である。
今後の方向
これらの効果にZ軸方向のインクリメンタルを加え、アイテムの加工ステップを可能な限り分解して行くと必要な瞬時の荷重はどんどん軽くなる。例えばモジュール20、PCD2000mmもの風力発電増速機用歯車の成形や高荷重を要すと考えられていたサイクロイド内歯歯車の成形にも道を開くものとなろう。
ほとんど放電加工に近いフレキシビリティをもった本機は工作機械と鍛圧機械のハイブリッドの性格を持ち、「プログラマブル内面成形機」と称することも考えられる。
個々にはアイテムに応じて複雑なプログラムを必要とし、その作成は転造盤メーカーひとりでは到底賄いきれない。被加工品の機能を熟知した本機のユーザー技術者、コンピュータシミゥレーションを活用した加工順や応力の事前把握の研究者、工具強度の強化を図る設計者、本技術の展開ストーリーを見越せるゼネラルマネージャ、等など多方面の人材の登場を切望している。
インテリジェントプレスの説明
緒言で述べたサーボプレスのインテリジェントな使用実例を紹介する。第8図に示すのは前方押出の足長さに関する制御である。素材長さの若干のバラツキにもかかわらず素材のコンテナ内への充填終了から実質押出に移る荷重の変化点を毎回把握し、演算による所定のハイトまでスライドを降下させ加工を終了する。演算により算出された分が足長さとなる。
第9図に示すのは従来素材を然るべき位置においてと言う点で困難であった工法であるが素材を運搬、把持しているフィンガーをパンチが素材を上下に挟んで保持するまで開放せずに待つと言う送り装置と一体となった運転プログラムで困難を解消している。
ここに使われているプレスは主シリンダの運転に電磁切替バルブ、配管、ホース、リリーフバルブ、が使われていない画期的なものである。この機構の詳細説明は次の機会に譲る。
- ^ 平成19年4月20日、特許第3947204号、株式会社 エムエイチセンター所有。
- ^ 青山 進、青山 剛; 塑性と加工 第50巻 第587号(2009-12)