新開発インターナル歯車の転造盤と演算運転サーボプレス
緒言
平成21年度の塑性加工学会技術開発賞(中小企業)を受賞した「新開発ヘリカルインターナル歯車の転造成形」のその後の状況と、近年弊社が力を注いでいるサーボモーター駆動を最大限活用した加圧加工中に得る数値情報を演算処理してその加工のプログラムを作成実行し自身で終了条件を決定するいわばフィードホワード方式のプレス加工システムを紹介する。
この2件は加工法としては一見脈絡が薄いようにも見えるが、共に近年発展のサーボシステムが事前に組まれたプログラム通りに作動するだけでは物足りなく、加工中に得る種々の情報を処理しながら加工を進めてゆくことにおいて新たなステージが開けるのではないかと考えて開発したものである。転造盤あるいは転造工法、さらにはプレス加工法の具体的方法以上に本稿では情報収集と演算処理に焦点をおいて述べたい。
新開発ヘリカルインターナル歯車の転造成形と転造盤の進歩ヘリカルインターナルギヤ
受賞対象となった転造盤[1]はその後少し進化して現在は図1に示すごとくコンテナ回転に関して完全な従動自由な状態からその回転情報のモニターが可能な仕様に発展している。タイミングベルトを介しているので割出し精度に関わるほどの剛性は持ち合わせてはいないが回転角モニターとしては充分で、工具と加工品の契合を一時的に解除して異なった組合せで再契合する程度の自発的コンテナ回転の制御は可能にしている。
第1図、コンテナ回転制御付き内歯車転造盤(クリックで拡大)
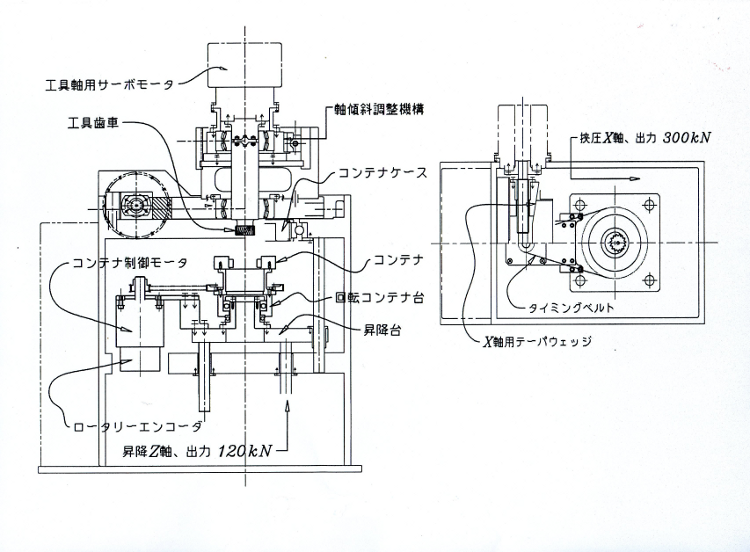
第2図、コンテナ部外観
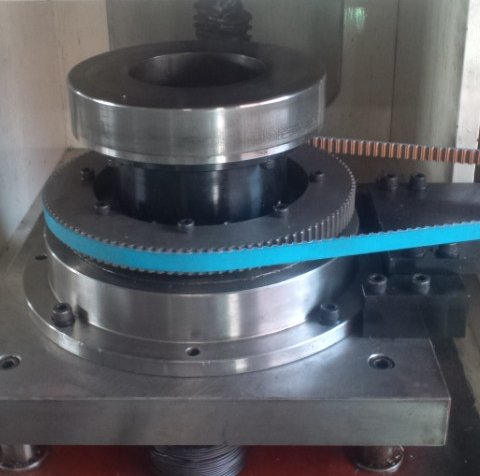
本転造盤による内歯車の転造を説明する。第3図に示すコンテナに素材を整合挿入してその内側から工具歯車を押し当てコンテナ内側との挟圧によって工具歯車の歯形部を素材の内側に転写することで内歯車を成形するのであるが、予め歯数に相当する溝が加工されていない場合は工具歯車の回転にコンテナが自由に従動するだけでは所定の歯数を正確に転写するにはかなりタイトな条件設定に基づく歯数設定用工具が必要であった。
第3図、歯車創歯転造の解説(クリックで拡大)
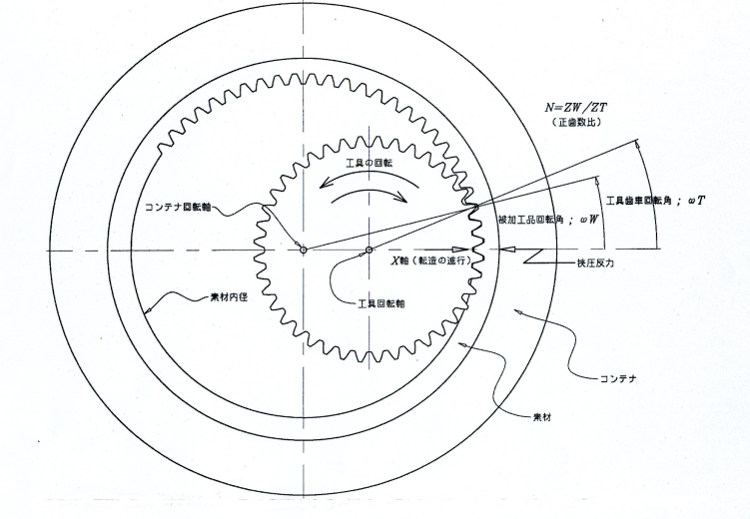
勿論先駆ける他の工程において予め歯数に相当する溝などが加工されている場合は分割精度が事前加工に委ねられてこの問題は避け得る。
ここではまったく平滑な内径の素材に正確に歯溝を刻み所定の歯数を得るための手段を説明する。第3図に示すごとく、素材内側に工具歯車を押圧しながら工具歯車をある回転範囲内を往復させる。この間の工具とコンテナの回転比が所望の歯数比に正確に一致するところまでX軸を進めてゆく。理論比に一致した回転比を保ちながら転写領域を拡大して行き最終的に全周に歯形を転写する。
予め定められたX軸位置まで転写を推進してゆくのでなく、素材内径などの微小とはいえ避けられないバラツキを吸収して、結果として正確な歯溝の配置を達成する。この場合のキーポイントは加工中に回転比を把握することにある。
関係する新たな所見
この回転比のモニターは別の所見をオープンにした。過去にスパーギアの転造はヘリカルギアにないぎこちなさを感じていたがこの回転比を微視すると契合回転の一歯ごとに従動側の遅速が見え回転速度を上げた場合の振動発生と関係している様である。最近ある諸元のスパーギアの転造で工具歯車がひと歯欠損の事故を発生したがこの現象も同根ではなかろうかと考えている。本転造を活用するには最低限のカミアイ率などがある種の要件となりそうである。
逆に考えれば過去の経緯からきた歯車諸元から脱して本転造工法に適した歯車諸元を用意することが可能ならばこの経済的な加工法を自家のものとするひとつの方法である。
この様な解析も加工中に得る情報から得る大きな効果で本稿ではこの点を強調したい。
本転造盤の活用方向
現在、ヘリカル歯車の転造成形は勿論であるがそれ以外にもこの新しい転造盤の活躍場所としてチャレンジされている分野は少なくない。多板クラッチのドラム、シンクロスリーブ、など内周に凹凸が存在するアイテムは少なくない。需要家各社の情報の壁は高くはあるが漏れ聞こえるアイテムは確実に増加している。
弊社が独自に開発しているのは内ネジの転造加工である。その試作サンプルを第4図に、使用した工具を第5図に示す。この加工は本転造盤の工具軸回転とコンテナ回転の相対回転角を強固に同一角に保持するロジックを作り工具のピッチと加工品のピッチを合わせて素材内径に転写せしめた結果成功したものである。同一の工具で大小2種類の内ネジが成形出来ているのは工具軸の公転半径を変えることでネジ径を成形している新しい工法を証明している。
本内ネジ工法の要点とする工具軸とコンテナ軸の相対回転角を強固に同一角に保持するということは工具軸もコンテナ軸も個々にはまったく回転の必要がないということなので、現在、工具軸もコンテナも回転しないX-Yテーブルが円弧運動をするだけの廉価版内ネジ転造機を試作中である。近々発売する新しい転造機は新しい機械を生み出そうとしている。新開発ヘリカルインターナル歯車の転造盤が文字通りであれば歯車以外に適応するはずがないが歯車も出来る新しい加工機と認識し、更に加工途中の情報を取り入れた運転ロジックを生み出せれば活用アイテムは無数に存在するように思われる。
第4図、同一工具で転造成形した内ネジ
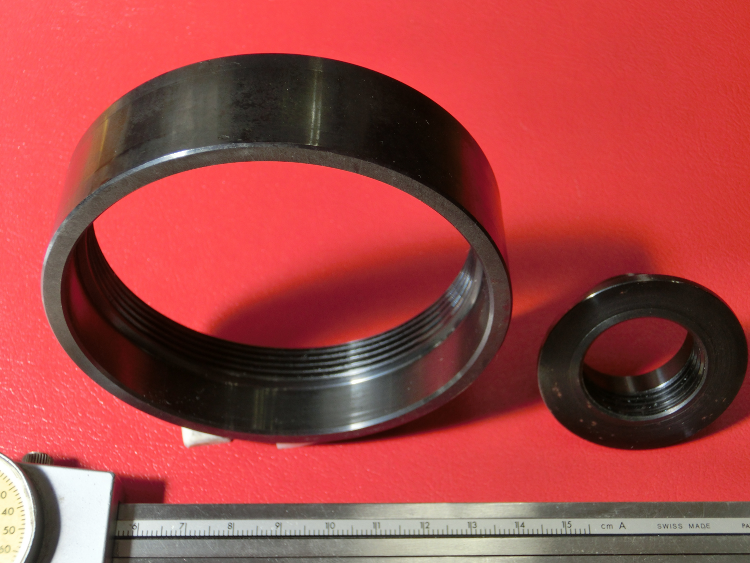
第5図、ネジ転造工具
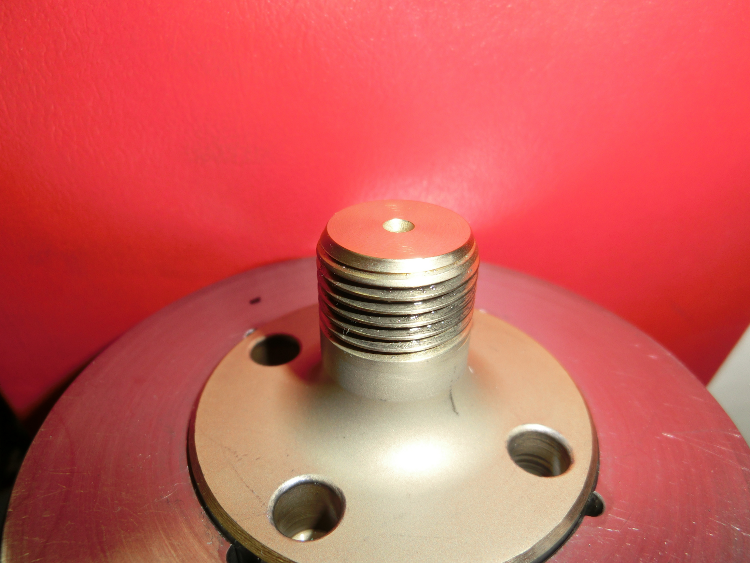
演算運転サーボプレス
同様にサーボモータを駆動源とするプレス機械はその速度、モーションを事前プログラム可能であるばかりでなく、その圧力作用側に正確な加圧力を知るためのロードセルを介するか、あるいは正確な油圧を計測、制御可能なシリンダ機構を有することで時間軸上のスライド位置と加圧力を相当細かく且つ正確に把握することができる。この機能を活用して得た加圧力曲線を数学的に処理し、自らの行動、あるいは行動の終了条件を設定し、知り得たことを表示する機能を有するプレスを紹介する。
その運転プログラムは活用すべき情報収集とそれを生かしたロジックにより個々に作成することになるが
第6図、展示機の外観
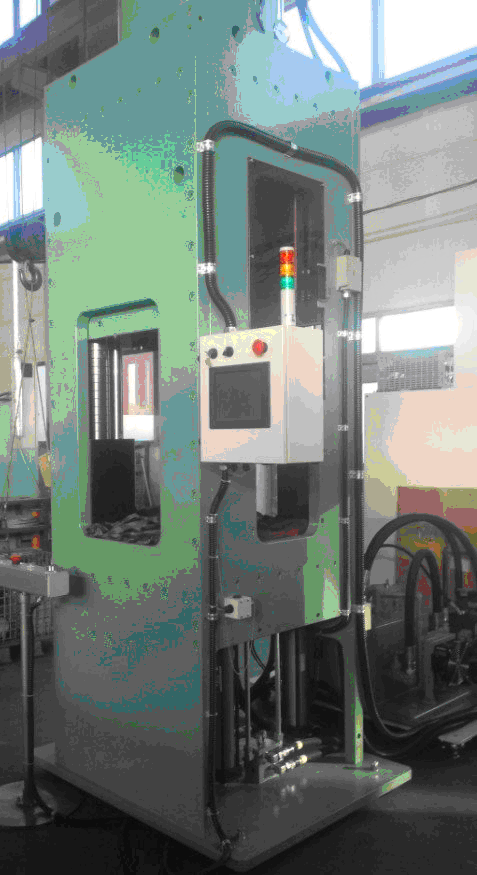
第7図、制御圧縮成形時のタッチパネル
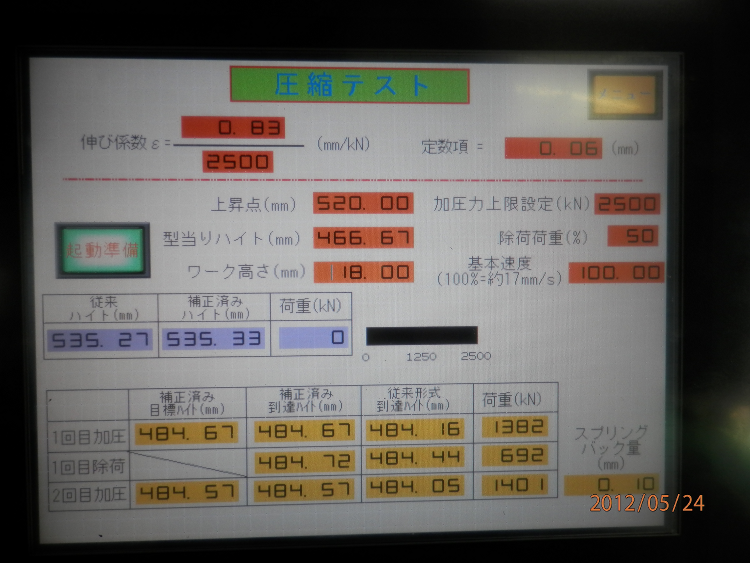
本日はその中の2~3の具体例を発表する。プレス機械のハード面においてはサージやノイズに惑わされることのない、具体的には切替バルブ、リリーフバルブ、圧抜バルブを使用しないハードを開発しなければならなかった。結果として小型、高剛性、静粛でインラインに相応しいピットレス機となった。現状小型はボールネジ仕様、200kN以上は油圧仕様で最大能力は6300kNである。
弊社展示機 MHP-2540(登録商標 'Majestic'[2])の仕様
本来はユーザー仕様で都度設計製作するものであるが標準機を常設展示している。
- 特徴
- 冷間鍛造用、高剛性、低騒音、省力、省空間、ピットレス、付加もうひとつの操縦桿。
- メインシリンダ(諸元)
-
22KW相当 サーボモータ駆動
加圧能力 2500kN
加圧力精度 ±0.5%
ストローク 400mm
アプローチ速度 177mm/sec
上昇能力 260kN
上昇速度 146mm/sec - 下部シリンダ(諸元)
-
能力 260kN
ストローク 200mm
上昇速度 148mm/sec
(下部シリンダをサーボ制御することも開発中) - 制御
-
スライド位置 - 加圧力 - 速度(加速度)- 制御
微分(再微分)加圧力曲線把握、自動演算終了
'Majestic' の活用例(1)、制御平圧縮
単純な平圧縮(アプセット)において目的とする被加工材の加工後高さ(H)を機械にインプット(タッチパネル上「ワーク高さ」)する。次いで素材をセットした後にスタートボタンを押せば、スライドは当然'H'が実現されるはずの位置(H1)まで降下する。このとき発生する加圧力の多寡からプレスの伸びや金型の縮小を類推相殺するための事前インプットがタッチパネル上段に表示されている。
図7.の写真では2500kNに対し0.83mmの相殺がなされていることを示している。以後のスライド位置はこの種外部状況の相殺済の値である。通常量産品の素材硬さ、型温度、潤滑条件の違いなどを相殺修正するにはこの機能だけで充分である。
ここでは第一段のスライド位置(H1)実現後一度スライドを上昇(実質減圧)させ、H1における加圧反力(P1)を半減させた加圧力(第二段)における位置(H2)を知り、この間のスプリングバック量(ΔH/2)から完全解放時のスプリングバック量(ΔH)を算出しする。勿論半減が80%減でも設定次第である。
この把握したスプリングバック量を相殺する第3段の最下降位置(H3=H1-ΔH)を実行することでかなりの正確さで鍛造品の厚み(H)が得られる。
同様のルーチンを繰返すか否かは目標寸法の精度にもよる。また、スライド位置と加圧力の関係はスライド速度が速いほど平衡状態とは違った値を示す。必要な速度を選べばよい。動画で紹介する運転時の精度は±0.02程度である。
第8図、に示すチャートは制御平圧縮時の加圧力―時間のチャートであるが、加圧力半減時の減圧中に情報をとることも可能ではあるが各段が解かりやすいように一段毎に圧力を解放している。第9図は加工品の厚み測定で±0.02を実現している。
情報はますます増える
前述のプログラムは素材の高さや体積、またプロポーションを問うことなく、指定した'H'を実現することで加圧作業としては完了しているが、この間に得られたスプリングバック量を活用することで驚くほど
第8図、制御平圧縮時の時間―加圧力のチャート
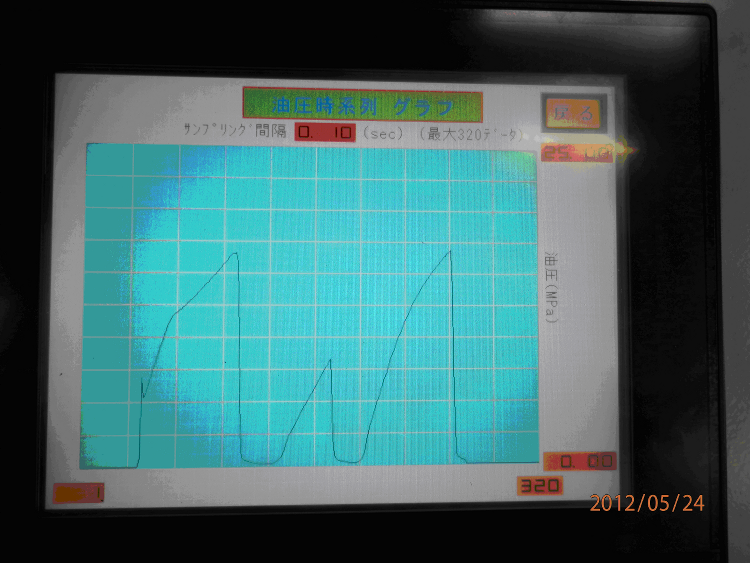
第9図、制御平圧縮品の厚み測定
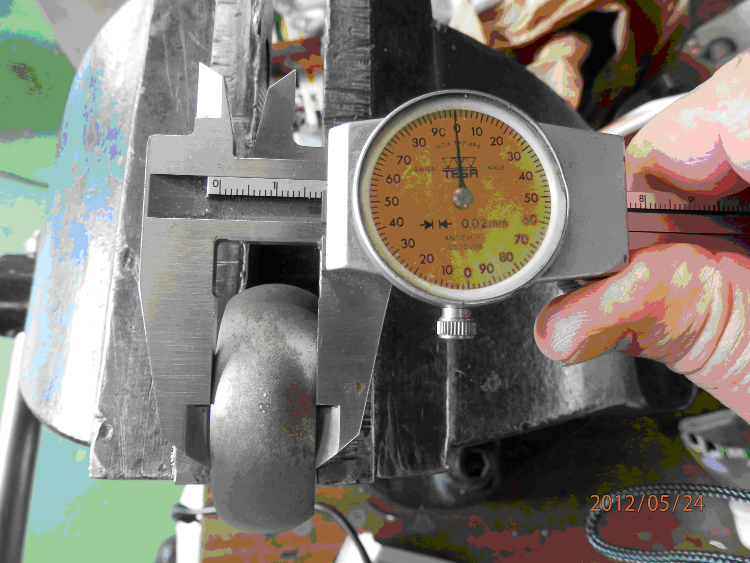
多様な情報を手にすることができる。例えば、
- ΔH/H から(材料のヤング率を知っていれば)H3における被加工材の変形抵抗Kfc(平均値)がわかる。
- プレス最下降位置(H3)におけるプレスの加圧力(P3)をKfcで除することで被加工材の面積(S3)がわかる。これは被加工材がいかなる2次元形状をしていてもともかくオールサムの面積ということで実効面積とでも言おう。この圧縮プログラムを被加工材の弾性変形領域内で処理すれば断面積推定方法として独立して使用することも考えられる。
- 被加工材の高さ'H' に前記'S3'を乗ずることで素材の体積が計算できる。比重を把握していれば当然重量も知ることになる。
- 'Kfc'は加工完了品の強度の面における品質保証の重要な情報である。
'Majestic' の活用例(2)、制御前方押出
例えば拘束前方押出においては、素材切断重量の多少のバラツキもプロポーションの違いも包含してコンテナ内に素材が充満するまでの過程の加圧曲線と、押出加工の加圧曲線との仮想交差点からその押出のスタートポイントを演算把握し、最終スライド位置を設定しプログラムを終える。情報のフィードホゥワードで押出部の長さを保証する工法である。
また、本工法の類似判では拘束前方押出よりも関与する部品が断然多い、鋲カシメ作業の品質保証にも活躍している。対象アイテムの内径に軸太りで吸収された後最終ヘッディングに共されるべく空中に残った鋲軸の長さを把握し、定められた圧縮比を実現する。この場合、圧力制御でなく圧縮寸法制御であり、なおかつモニターした最終圧力を品質保証の源にしている。
本機はこの各種データを保存し品質保証のバックアップ資料とすると共に、運転直後に詳細チャートをタッチパネル上に提示する機能は加工法開発のためのツールとして好評である。
更なるハードの充実
現在本機は更なる発展を成しつつある。下部シリンダをサーボ制御することで下部シリンダを可変カウンタークッションとする新しい制御前方押出を開発中である。押出開始直後には必要であったカウンター力を順次減少させ、押出の進行に応じた必要なカウンター圧力を制御し、瞬間瞬間の押出条件を常に一定に保持することで、例えばネジレ歯車のネジレ角や歯厚をなりゆきにまかさずコントロールすることを目標にしている。
上記以外にも何らかのロジックを考案し、加圧加工中に何らかの情報を得、その情報を直ちに活用してその後の運転に寄与せしめれば都度発明に繋がることかも知れない。そのロジックを実演できるプレス機械を提供して行きたい。